Understanding Fatigue Failure in Welded Structures
Admin • July 4, 2018
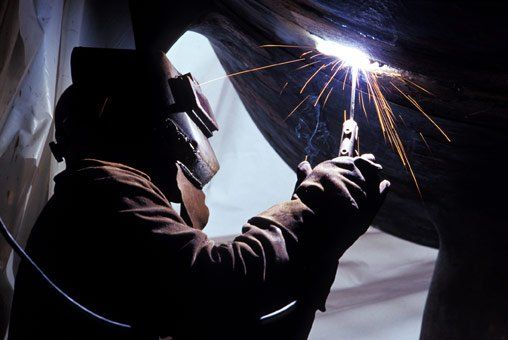
Welded joints present several advantages, among them a lighter weight and aesthetic appeal for metal structures. However, welds tend to be brittle, and any slight failure of the joint can result in serious accidents. Mitigating fatigue-related failure in welded structures should be a priority for the welder and the end-user.
Read on to learn more about fatigue failure, options for improving the strength of welded structures, and the critical role of an experienced welder.
Basics of Fatigue Failure
Fatigue can be defined as the formation and propagation of small cracks on a welded structure due to continued application of stress.
Fatigue failure takes place in two phases. The first phase constitutes the formation of cracks and the second phase entails propagation of cracks.
If appropriate measures are not taken following the initial formation phase, cracks can increase in size and propagate within a short period of time, thereby drastically reducing the load-carrying capacity and efficiency of the structure in part or as a whole.
Fatigue failure can affect just about any type of welded products including industrial, construction, agricultural, manufacturing, and mining equipment.
Causes of Fatigue Failure
Fatigue failure is less a result of the strength of the metal and more a result of welding technique. Factors such as inadequate preheating, trapped hydrogen or slag, incomplete joint fusion, and joint porosity can compromise the integrity of a welded joint.
Fatigue can be defined as the formation and propagation of small cracks on a welded structure due to continued application of stress.
Fatigue failure takes place in two phases. The first phase constitutes the formation of cracks and the second phase entails propagation of cracks.
If appropriate measures are not taken following the initial formation phase, cracks can increase in size and propagate within a short period of time, thereby drastically reducing the load-carrying capacity and efficiency of the structure in part or as a whole.
Fatigue failure can affect just about any type of welded products including industrial, construction, agricultural, manufacturing, and mining equipment.
Causes of Fatigue Failure
Fatigue failure is less a result of the strength of the metal and more a result of welding technique. Factors such as inadequate preheating, trapped hydrogen or slag, incomplete joint fusion, and joint porosity can compromise the integrity of a welded joint.
Inadequate preheating
Preheating improves the structural characteristics of a weld, minimizes the risk of cracking, reduces weld brittleness, and decreases the amount of metal shrinkage, which can result in excessive stress and breakage.
Trapped Hydrogen
Miniscule hydrogen ions, released during the welding process, can migrate from the weld joint and combine to form hydrogen gas along the fissures of the parent metal. The presence of hydrogen gas applies stress to the metal and increases the risk of cracking.
Porosity
The entrapment and freezing in of gaseous contaminants such as oxygen, nitrogen, and hydrogen in the metal substrate can result in the formation of holes on the weld. With time, these holes could result in breakage of the metal structure.
Incomplete Joint Fusion
Incomplete joint fusion occurs when one side of the weld joint is not properly fused into the weld. This may result in a number of imperfections that may reduce the load-carrying capacity of the joint.
Mitigation of Fatigue Failure
While all welded structures eventually succumb to wear and tear, weld improvement techniques can extend the life of the welded structure and mitigate catastrophic cracking.
Weld improvement techniques fall into two categories - techniques that improve weld geometry and those that reduce residual stress.
Weld Geometry Improvement
Sharp corners, holes, and decreased cross-section areas may increase stress concentration. Weld geometry improvement techniques seek to reduce or control stress concentration on weld joints.
Common geometry improvement techniques include grinding the weld toe using a bur or disc grinding machine, using Tungsten Inert Gas (TIG) to re-melt the weld toe, and plasma dressing.
Residual Stress Reduction
Residual stress results from thermal expansion caused by the temperature differential between the weld joint and the parental metal.
Techniques such as thermal stress relief, vibratory stress relief, hammer peening, shot peening, and ultrasonic hammer peening may help to mitigate the effects of residual stress.
Welded joints will yield to stress over time, necessitating regular monitoring and maintenance of metal structures. Even then, good welding practices from the get-go can help alleviate the risk of premature and potentially catastrophic cracking of welded structures.
At 3-B Welding LLC , welding is our specialty. Using superior tools, we provide high-quality equipment repairs and custom fabrication services for all types of projects. Get in touch with us today for long-lasting welding solutions.
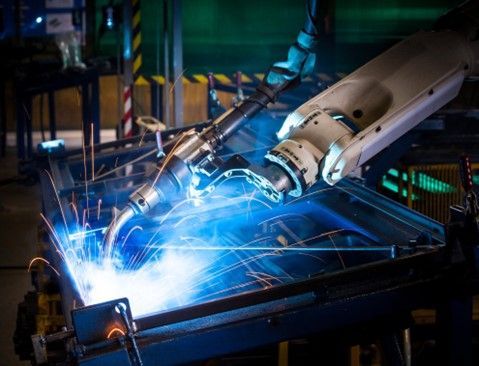
Dive into the latest innovations in welding technology, including advanced arc welding, laser welding, ultrasonic welding, and hybrid techniques. Learn how automation, smart welding systems, and virtual reality training are transforming the industry by enhancing precision, efficiency, and safety in welding processes.
If you are embarking on a construction project, read our blog to learn the benefits of working with a mobile crane service for your heavy lifting needs.
Read this informative article to learn how Gas Metal Arc Welding (GMAW) plays a pivotal role in commercial projects across various industries.
Welding services play a pivotal role in agricultural industries. Read our blog to learn how you can utilize welding services on your farm.
Understanding and reading crane load capacity is paramount in ensuring safe and efficient lifting operations. Read on to learn more.
Damage to oil field drills can cost you money through lost revenue and repair or replacement costs. Read on to learn more helpful preventative measures.