2 Common Causes of Low Aggregate Conveyor Productivity
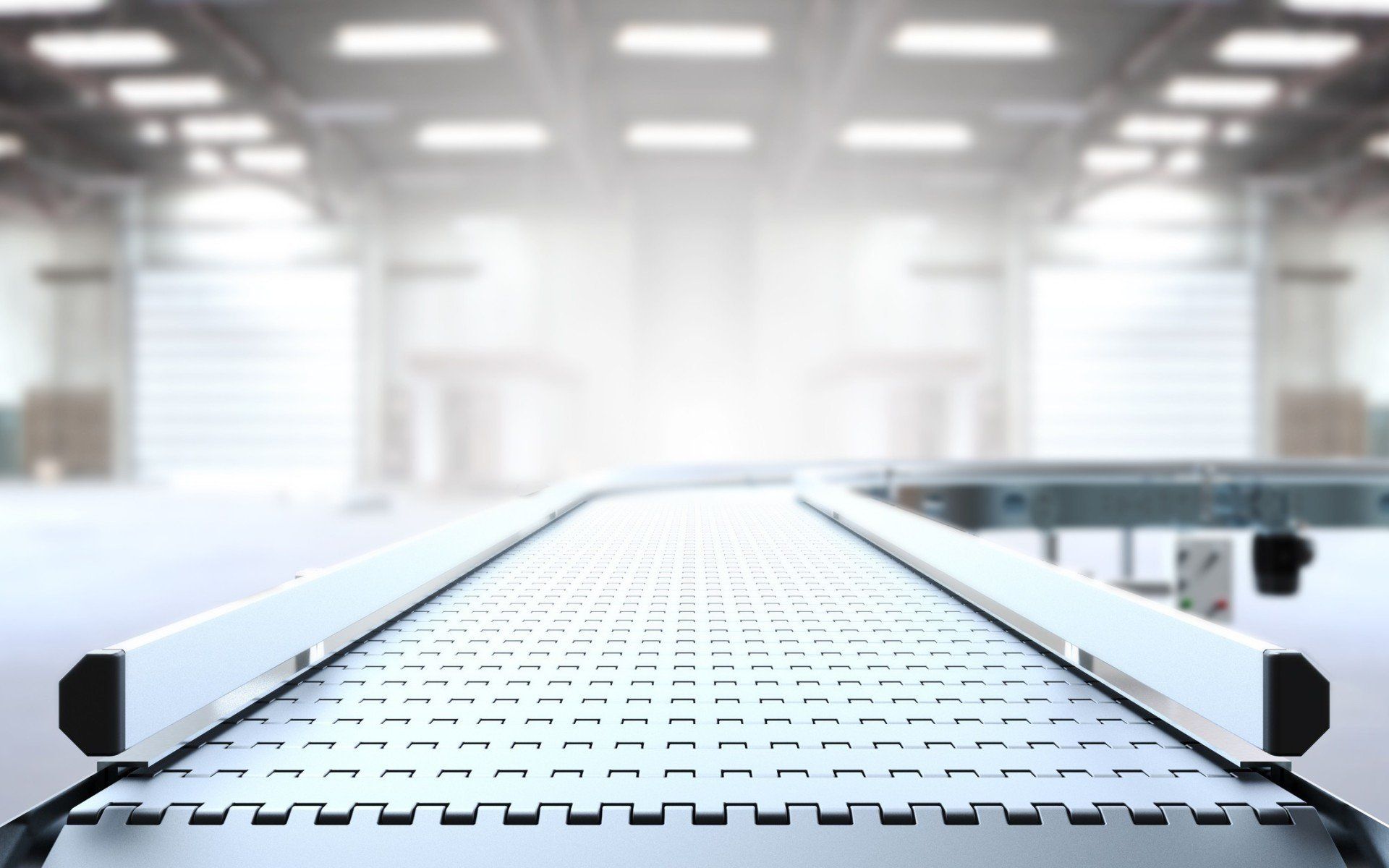
Conveyors play a central role in facilitating smooth, efficient production runs of aggregate handling. Whether your material is gravel, sand, or precious minerals, one or more conveyors need long, predictable run times to maintain a high level of productivity.
Unfortunately, several things can go wrong to interfere with or completely halt that flow. Equipment failure, human error, and other factors often result in conveyor damage and lost time. Here are two common causes of low conveyor productivityin the aggregate industry.
1. Poor Conveyor Belt Tracking
Because the belt track is in constant contact with rough product, the belt can malfunction and track poorly. A belt that tracks badly may start to wear unevenly, experience loss of tension, stretch or strain too much, harm other conveyor components, and possibly injure nearby workers.
Many factors influence a conveyor belt enough to throw off tracking:
- Operation on uneven ground
- Belt spliced incorrectly
- Uneven material loads
- Material build-up
- Pulleys and idlers not square to conveyor
2. Transfer Point Spillage
When several conveyors and loaders are in use in a single system, your operation is at risk for transfer point spillage. Spillage occurs as material loads onto or unloads from a conveyor. Material is wasted over time, which adds up to significant amounts annually. Additionally, workers must stop and clean up excess materials that spill.
You may experience different types of spillage. To help prevent spillage at your operation, employ one or several of the following methods:
- Place loads in the center of the belt. Each load must be consistent and uniform. To better direct loads to the center, use deflectors, baffles, liners, or a curved loading chute.
- Lessen the impact of loads onto the conveyor. Continuous high impacts cause belt damage. Instead, place impact cradles below the conveyor or set up impact idlers with rubber-cushioned rollers at key transfer points.
- Stay on top of belt scraper tension. Belt scrapers at key locations and angles need a certain range of tension to work effectively. Sophisticated systems have a device that reads the tension. You need to check the reading regularly to prevent material carry back, spillage, belt mistracking, and worn components.
- Maintain appropriate skirt boards to help contain spillage. Skirt boards should extend from the loading chute to far enough along the belt where material reaches full belt speed. Make sure the skirting is near enough the belt for rubber or urethane seals to prevent spillage into any gaps.
- Reinforce seals with wear liners to avoid belt sag and trapped materials. Wear liners protect the seal from the full force of loads.
Other components of a conveyor can wear out over time due to excessive use. Idlers, or rollers, that carry and return on a conveyor rely on seals and bearings. Pulleys must drive, change direction, or maintain motion of the conveyor. In many instances, conveyor downtime is the only good time to replace or repair many conveyor components like idlers, bearings, and pulleys.
Sometimes maintenance and good operation strategies are not enough to prevent a broken component. You need to be able to repair or replace a part quickly. 3-B Welding, LLC., is qualified to repair or rebuild important aggregate components on-site. Call us and ask how we can help keep your aggregate operation running smoothly.
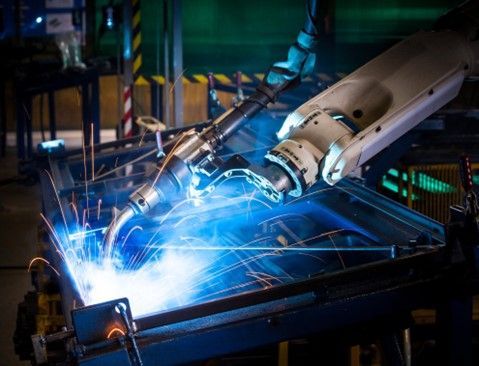