Weld Failure Risk: Things to Ask Your Welder
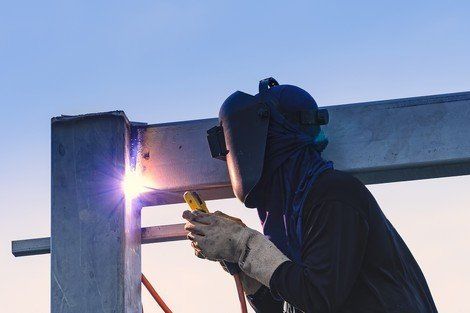
Metal fabrication is a complex process that involves careful bending, shaping, preparing, and welding. When you work with a welder to complete your manufacturing needs, you should understand what constitutes quality welding. After all, many different factors can weaken the integrity of a weld.
If you find that your weld joints aren't holding up as they should, you should consider a few things to discuss with your welder.
Was the Metal Properly Cleaned?
Clean surfaces are essential to a strong weld bond. Any kind of debris, dirt, oxides, or other particles on the metal will disrupt the weld, creating a final weld that is porous and not uniform. Since any porous nature in the weld means pockets of weakness, you want to avoid anything that will result in a porous weld.
Metal must be cleaned and adequately prepared prior to welding to avoid pores. This means grinding or sanding the metal to remove anything on the surface, followed with cleaning with an acetone-based solution to remove the dust left behind as well as any protective coating on the surface of the metal.
Was the Metal Heated Evenly?
You can't weld hot material to cold metal. For a weld to truly bond with the metal on both sides, both of those sides need to be heated evenly. If either side, or even both sides, aren't heated enough, the weld will not properly bond. This leads to a weak final weld that is likely to fail.
Even if both sides of the actual weld location were heated, you may still have problems associated with metal distortion if that heat passes to any area beyond the weld joint. Distorting the metal can actually shift the alignment of the metal at the weld site, creating stress on the weld joint. Stress on the joint increases the risk of cracking in the weld, ultimately leading to weld failure.
Ask your welder about their heating preparations to ensure that both of the metals were adequately heated. He or she should also account for any distortion by ensuring proper joint alignment before starting the weld.
Was the Metal Annealed?
Heat isn't the only temperature-related factor that affects weld quality. Cooling is also important. When the metal is cooled too rapidly, it creates stress that puts pressure on the weld joint internally. This leads to cracks inside the weld.
Your welder should prevent this type of integrity issue by annealing the metal. The weld area will need to be heated again, but to a lower temperature than when it was welded. Then, the metal and the weld should cool gradually on its own to ease any stress caused by the initial heating and cooling cycle.
How Is Oxidation Prevented?
Oxidation can interfere with the bond required for a strong weld. When metal gets hot, as it does during welding, it oxidizes. That natural oxidation disrupts the welding process if not prevented. There are two primary ways that welders prevent oxidation from the welding process.
Gas shielding, using argon gas, creates a barrier that eliminates any oxygen in the weld area. The argon gas is released in the immediate area of the weld to draw oxygen away from that space.
As an alternative, a flux rod can also prevent oxidation. Flux rods contain carbon, and that carbon will bond with the oxygen before the metal can, preventing any oxidation in the weld area.
You should work with skilled welders to ensure strong finished products for your projects. If you have welding tasks that you need to have completed, or you have any questions about the process, contact us at 3-B Welding, LLC.today. We will be happy to help you with your welding needs.
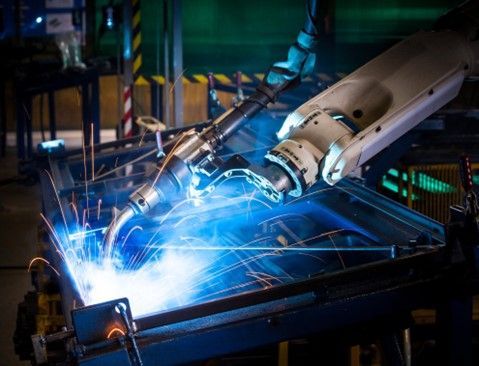