3 Habits That Force GET Repair and Replacement in Earth Movers
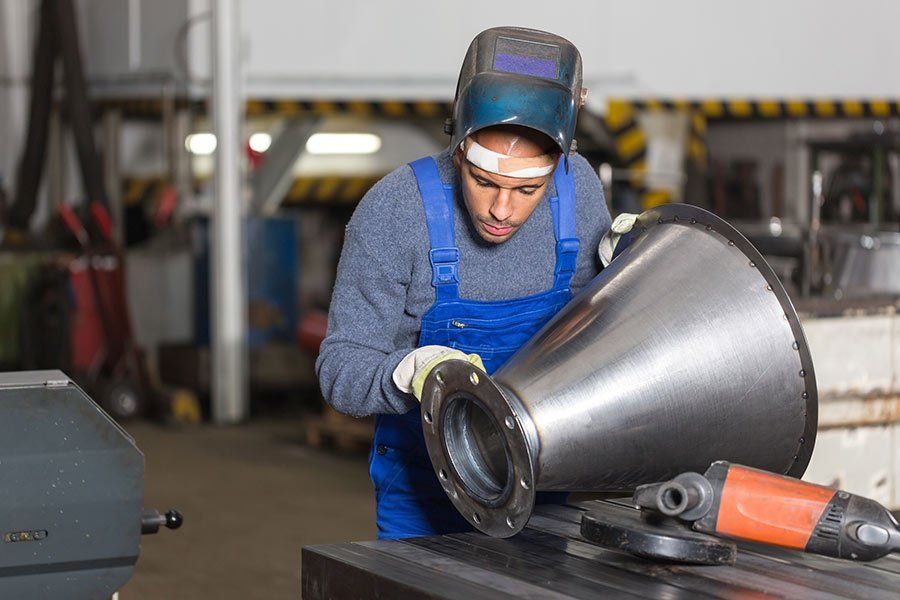
Many heavy equipment earth movers use ground engaging tools (GET). These tools are special metal attachments designed to reinforce and extend the life of expensive working blades and buckets. Side wear plates, sidecutters, teeth, horizontal bottom wear plates, and base edges all work to fortify buckets and blades for a range of digging applications.
However, a machine is only as good as its skilled operator and maintenance team. Several factors often shorten the life of GETs and cause unnecessary tool replacement. Read on to discover three habits that force frequent GET replacement.
1. Wrong Operating Technique
Operator technique is responsible for how slowly or quickly GETs wear out. Consistently employing the wrong techniques accelerates wear to GETs. Consider how the following improper techniques hurt operations, and how to resolve them.
Excavators
Off-center pile approach or swinging in from the side harms bucket corners and sides and lessens the amount of fill in a bucket. Instead, enter a pile squarely. Doing so minimizes corner loading, wears GETs evenly, and ensures full buckets.
Excessive pry force or too much ground contact stresses GETs and slows down production. Break hard materials first with a different tip or adapter, and then continue with a standard bucket. Position the bucket to avoid ground contact and make the tips do the heavy work.
Wheel Dozers
A blade tipped too far back wears the back of the sole plate, while a blade too far forward can cause a sudden and deep penetration. These angles put the moldboard at risk for damage and wear. Place the back of the blade perpendicular to the ground so the sole plate rests flat on the ground.
Pushing the machine too fast creates a dusty, bumpy environment and produces an inefficient surface finish. Slow down to ensure more even, thorough passes with less risk of bumps and dust.
2. Skip Daily Inspections
Careful attention to GETs should be part of overall hydraulic and other system inspections. Because they receive the brunt of all the action, check daily for signs of wear such as:
- Scalloping at base edges
- Missing retainers and tips
- Bent or broken corner gussets
- Folded in corners
Wear in these and other critical areas indicate it may be time for adjustment or replacement. Sometimes you can rotate tips and cutting edges that experience uneven wear. For example, rotate worn outer or corner bucket tips to the middle. Flip tips over to take make the most of remaining sharp edges.
Lost tips should be immediately replaced as even one missing tip lowers the digging ability of a machine. Plus, base edge wear escalates. GET wear is normal, but don't let cutting edges and tips run beyond the recommended service life and fail.
3. Wrong Tool for Materials
Different GETs possess unique characteristics designed to give them an edge for their intended application. Tool alloy, shape, length, thickness, and hardness help your machine better work with certain materials.
The wrong tool for the materials at a site could result in tool wear and failure. Highly abrasive or impacting materials wear differently than softer, less abrasive material. For example, granites, basalt, and gravel are more wearing than coal, sand, and loam.
Instead, carefully choose the right protection and type of GET when you anticipate encountering rougher, more abrasive materials and loads.
Sometimes regular operation results in sudden metal failure or other adverse conditions despite good operation habits. When you're left without adequate GET replacements, you need a reliable option to keep production moving. Mobile welding and other heavy equipment services are available from 3-B Welding, LLC . Call us and find out how to add our services to your existing operation.
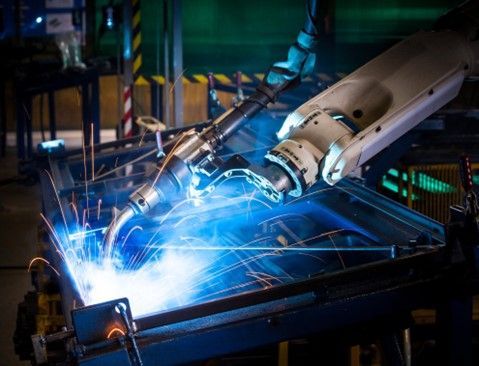