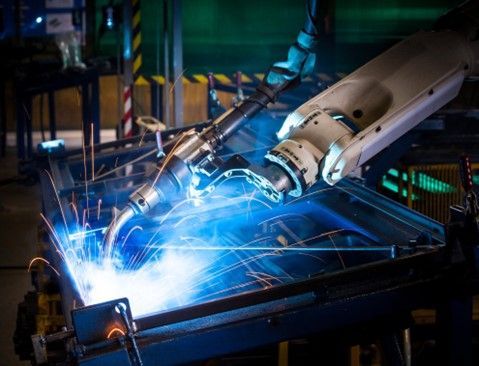
The deafening silence of a piece of heavy machinery is a contractor's worst nightmare. If your equipment isn't up and running, you are losing valuable time and money. It is difficult to move large pieces of equipment into a shop for repairs, so many contractors rely on field repairs to restore their heavy machinery to working condition.
Field welding can be a great tool used to address broken steel components on your large machines. The conditions in the field can't always be controlled, but an experienced technician will be able to use three important steps to help prepare the weld joint for lasting success when making repairs in the field.
1. Choose the Right Filler Material
The most critical step in joint preparation for field welding services is the selection of the right filler material. The replacement or filler material that is used to make repairs can have a direct impact on the durability and longevity of the weld joint.
Several factors must be taken into consideration when selecting a filler material. A technician will need to evaluate the chemistry and mechanical properties of the parent material before completing the weld joint.
The tensile strength of the filler material should always be the equivalent of the lowest tensile strength of the parent material. This will allow dilution from the welding process to strengthen the filler material as the weld joint is formed. The chemistry of both the filler and the parent materials must be complementary to ensure maximum adhesion.
2. Clean the Joint
Once the proper filler material has been selected, the second step in joint preparation for field welding is to clean the joint. Any dirt or debris that remains in the joint could compromise the integrity of the finished weld. Any rust, oils, or paint present near the weld joint must be ground down and removed.
Any loose dirt or debris should be wiped away from the surface of the parent material with a lint-free cloth. The cleaner the surface of the parent material is prior to welding a new joint, the less likely it is that the weld will show signs of increased porosity (like cracking or splitting).
Equipment that is repaired while still in the field must be carefully cleaned before welding occurs to produce a strong and durable weld joint.
3. Preheat the Weld Area
A hot welding arc cannot successfully be applied to cold steel. The differences in temperature will lead to imperfections in the weld. The easiest way to resolve temperature differences between the weld area and the welding arc is to preheat the parent material.
Preheating eliminates any oxygen, hydrogen, or other gases that might compromise the integrity of your weld. Without the removal of these gases, you may see shrinkage stresses, distortion, or severe cracking once the weld joint is complete.
An oxyfuel torch is typically used to preheat heavy equipment that must be repaired in the field. The torch will produce a wide flame that will increase the temperature of the parent material to create a malleable surface for welding. Joints that have been preheated are capable of withstanding more use than weld joints that are completed without preheating.
Repairing a piece of heavy machinery in the field is often the most affordable and efficient way to get your equipment back up and running. Many field repairs require the use of welding techniques that restore the integrity of a machine's metal components. It's critical that the weld joint undergoes proper preparation if you want the repair to last.
Contact3-B Welding, LLC, for your field repairs, and you will know that your repaired weld joints will last.